OSCILLATING SHUTTLE LOCKSTITCH MACHINE
DESCRIPTION
¶ Machine No. 31-15 makes the lock stitch and is intended for stitching clothing, cloaks, suits, skirts, shirts, etc.
Speed
¶ The maximum speed recommended for Machine No. 31-15 is 2200 stitches per minute. ¶ The machine should be run somewhat slower than the maximum speed at first until the parts which are in movable contact have become glazed by their action upon each other.
Needles
¶ Needles for Machine No. 31-15 when used on the power table are of Class and Variety 16 x 87 and when used on foot power stand are of Class and Variety 16 x 73. ¶ The needles are furnished in sizes Nos. 14, 16, 17, 18, 19, 21, 22 and 23. ¶ The size of the needle to be used should be determined by the size of the thread which must pass freely through the eye of the needle. ¶ If rough or uneven thread is used, or if it passes with difficulty through the eye of the needle, the successful use of the machine will be interfered with. ¶ Orders for needles must specify the quantity required, the size number, also the class and variety numbers separated by an x.
The following is an example of an intelligible order:
“100 No. 18, 16 x 87 Needles.”
¶ No other needles will give as good results as those furnished by the Singer Sewing Machine Company.
SIZES OF NEEDLES | CLASSES OF WORK | CLASSES OF WORK SIZES OF COTTON, LINEN OR SILK |
14 | Shirtings, Sheetings, Calicoes, Muslins, Silks, Dress Goods and all classes of general work. | 60 to 80 Cotton A and B Silk |
16and17 | All kinds of heavy Calicoes, light Woolen Goods, heavy Silk, Seaming, Stitching, etc. | 40 to 60 Cotton C Silk |
18 | Tickings, Upholstery, Woolen Goods, Trousers, Boys’ Clothing, Cloaks, etc. | 30 to 40 Cotton D Silk |
19 | Heavy Woolens, Tickings, Bags, Heavy Coats, Trousers, and Heavy Clothing generally. | 24 to 30 Cotton E Silk 60 to 80 Linen |
21 | Bags, Coarse Cloths and Heavy Goods. | 16 to 20 Cotton 40 to 60 Linen |
22and23 | Extra Heavy Work. | 8 to 16 Cotton 24 to 40 Linen |
To Ensure Perfect Action of the Machine
¶ The balance wheel must always turn over toward the operator
Do not run the machine with the presser foot resting on the feed without cloth under the presser foot. ¶ Do not run the machine when both bobbin case and needle are threaded unless there is material under the presser foot. ¶ Do not try to help the machine by pulling the fabric lest you bend the needle; the machine feeds the work without assistance. ¶ The slide over the bobbin case should be kept closed when the machine is in operation.
Thread
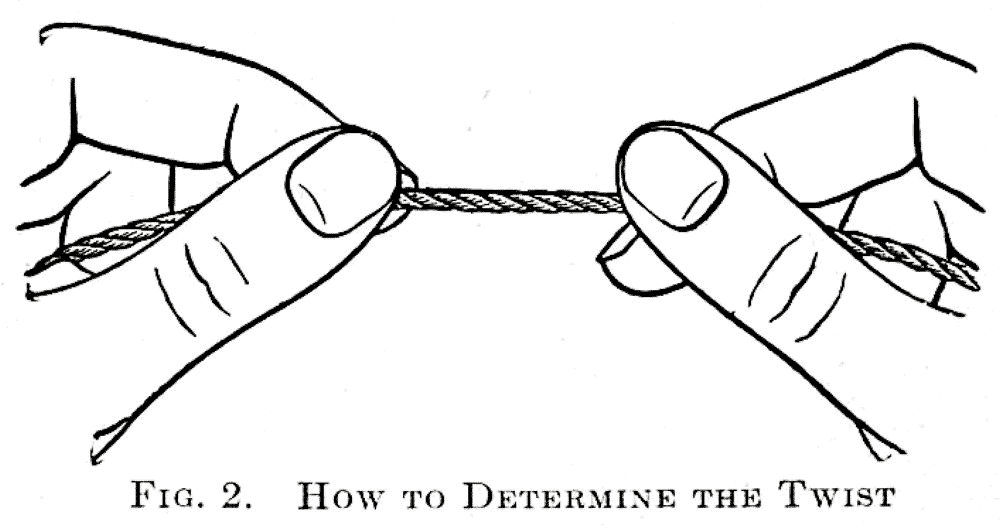
¶ Left twist thread should be used in the needle. Either right or left twist thread can be used in the bobbin. ¶ Hold the thread as shown above. ¶ Turn the thread over toward you between the thumb and forefinger of the right hand; if left twist, the strands will wind tighter; if right twist, the strands will unwind.
To Remove the Bobbin
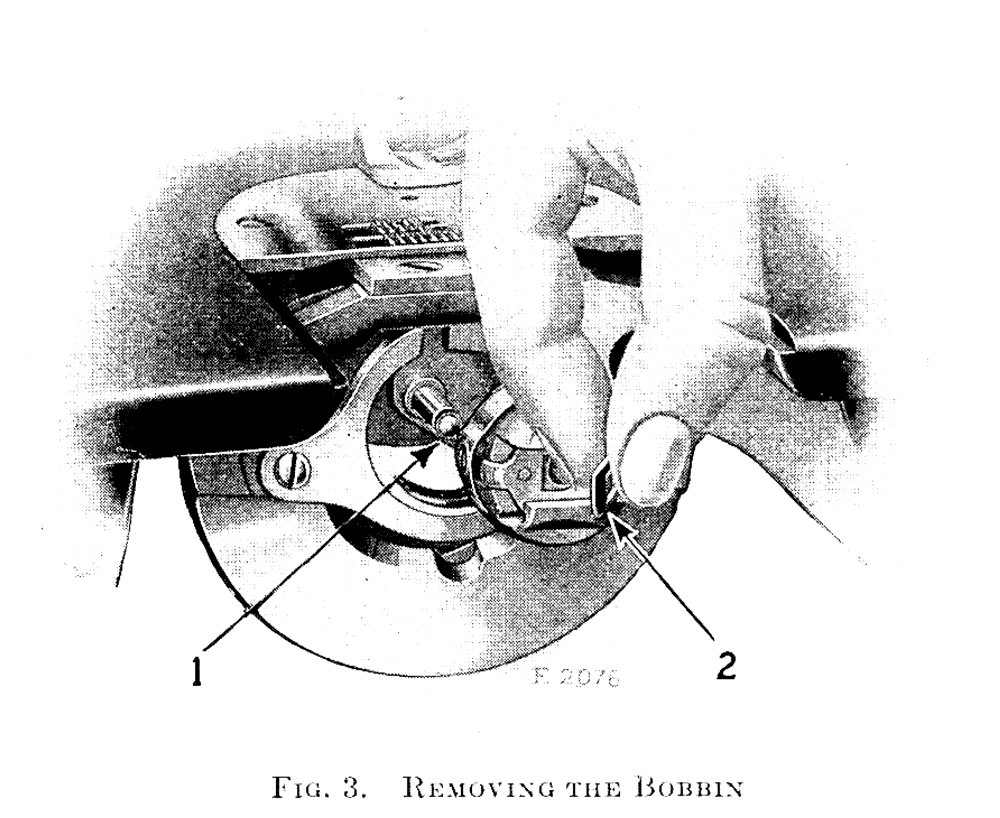
¶ Turn the balance wheel over toward you until the needle moves up to its highest point. ¶ Draw out the slide in the bed of the machine, reach down with the thumb and forefinger of the left hand, open the bobbin case latch (2, Fig. 3) and lift out the bobbin case. ¶ While the latch remains open the bobbin is retained in the bobbin case. ¶ Release the latch, turn the open end of the bobbin case down- ward and the bobbin will drop out.
To Wind the Bobbin
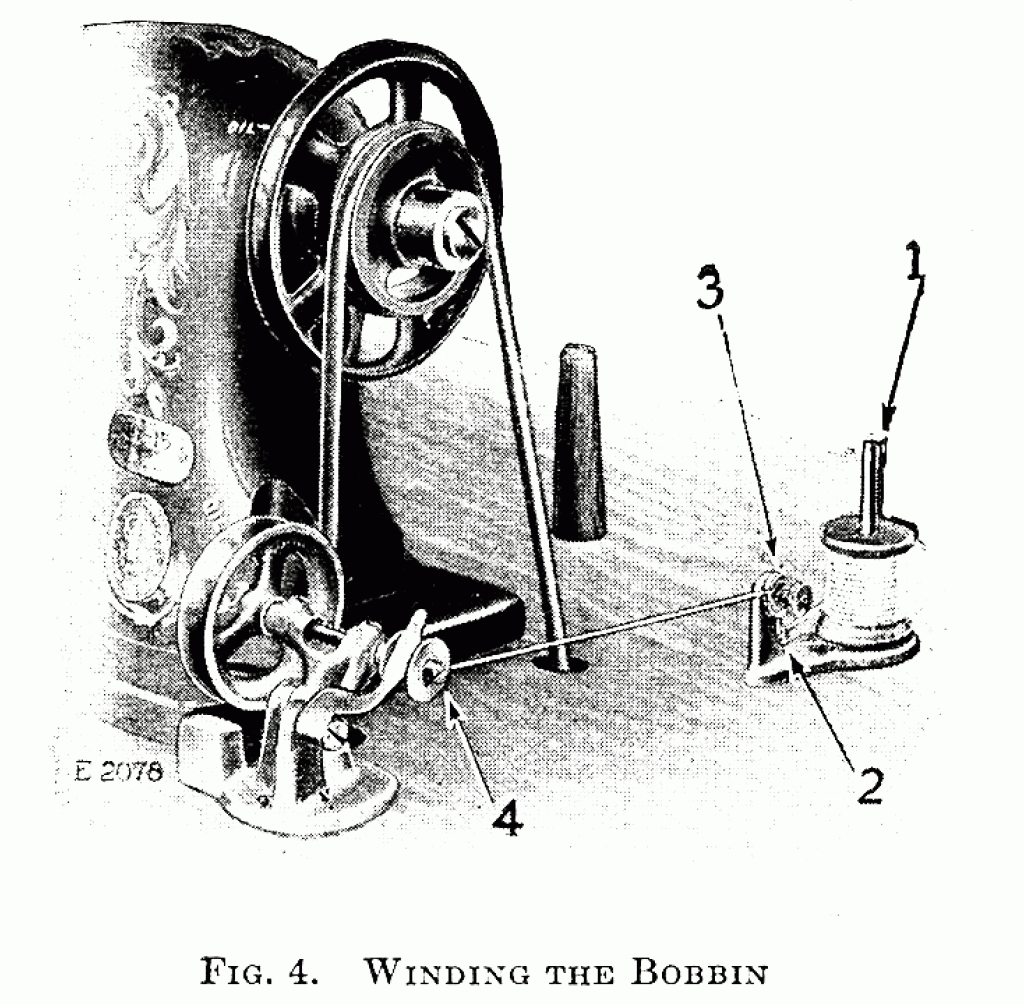
¶ Fasten the bobbin winder on the table at the right of the machine with its pulley in front of the machine belt so that when the pulley is pushed back it will come in contact with the belt. ¶ Fasten the spool holder for the bobbin winder near the back edge of the table with its tension bracket toward the front and the tension discs and spool pin directly in line with the centre of the bobbin on the bobbin winder spindle. ¶ Place the bobbin on the bobbin winder spindle (4, Fig. 4) and push it up closely against the shoulder, having the small pin in the spindle enter the slot in the bobbin. ¶ Put the thread on the spool pin (1, Fig. 4) of the bobbin winder spool holder, lead the thread under the wire thread guide (2, Fig. 4) on the tension bracket, up and over from back to front between the tension discs (3, Fig. 4); wind the end of the thread around the bobbin a few times and push the bobbin winder pulley over against the machine belt, then start the machine. ¶ When sufficient thread has been wound upon the bobbin, the bobbin winder wili stop automatically. ¶ Bobbins can be wound while the machine is stitching,
To Thread the Bobbin Case
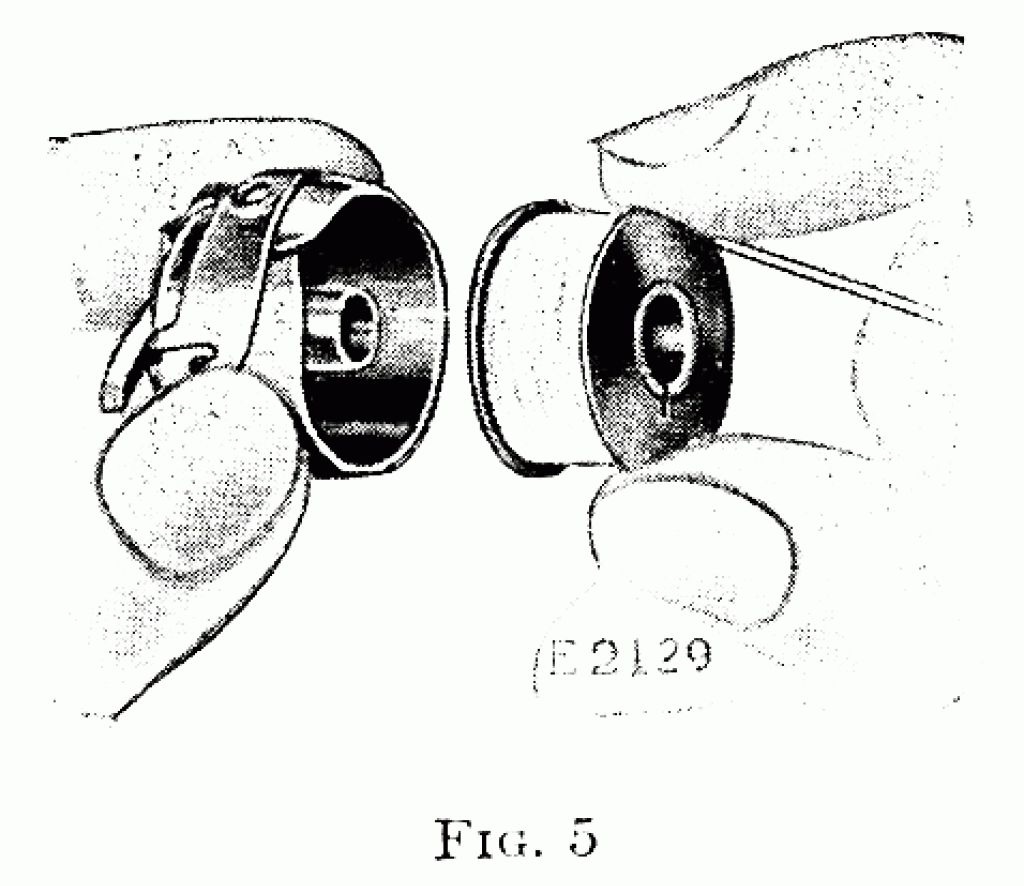
¶ Hold the bobbin between the thumb and forefinger of the right hand, the thread drawing on top from the left toward the right (see Fig. 5).
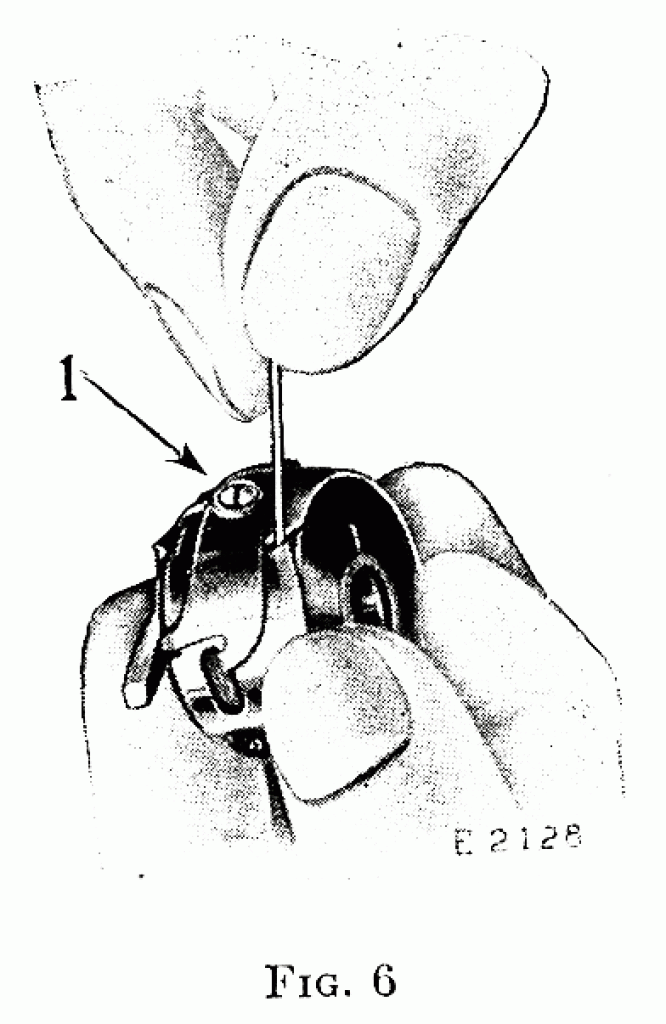
¶ With the left hand hold the bobbin case as shown in Fig. 5, the slot in the edge being near the top, and place the bobbin into it.
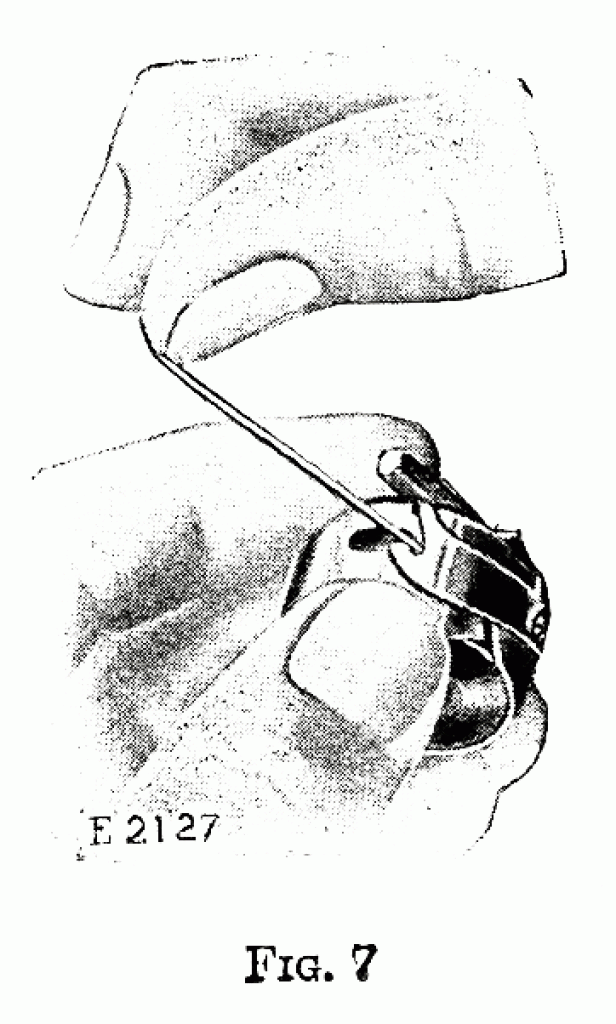
¶ Then pull the thread into the slot in the edge of the bobbin case (see Fig. 6), draw the thread down under the tension spring and into the delivery eye at the end of the tension spring (see Fig. 7).
To Replace the Bobbin Case
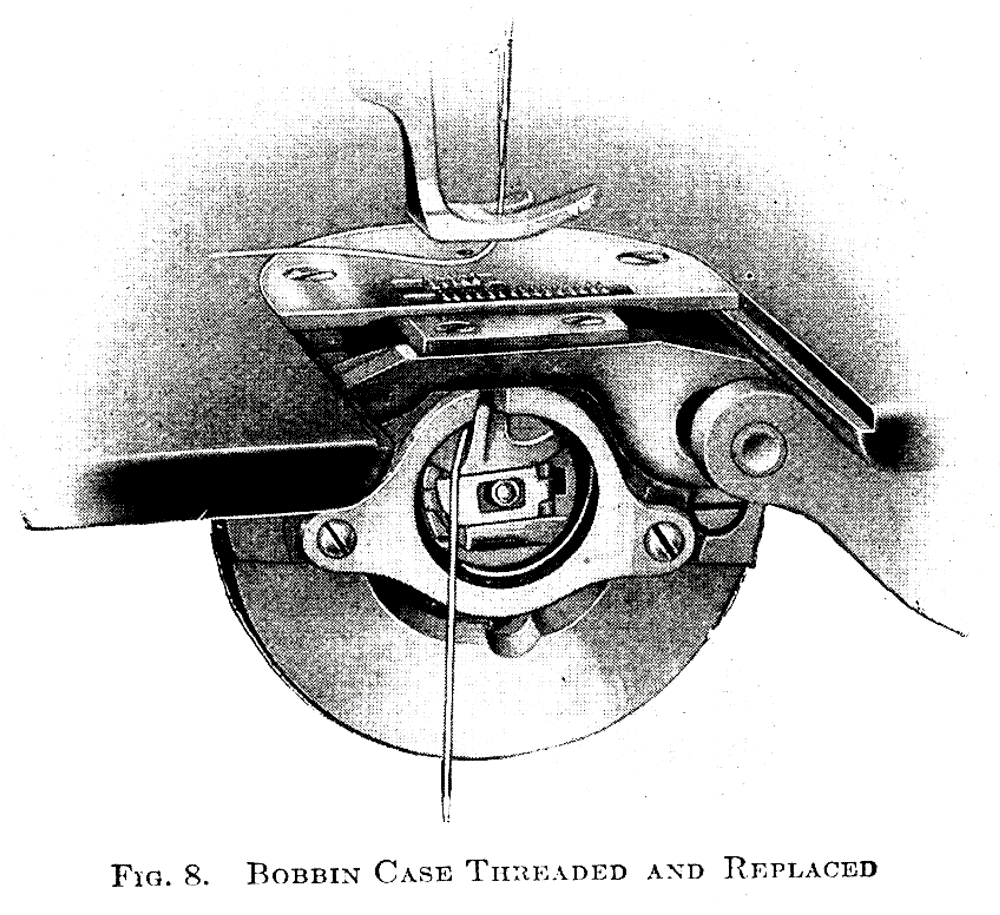
¶ After threading take the bobbin case by the latch holding it between the thumb and forefinger of the left hand; place the bobbin case on the centre stud (1 Fig. 3) of the shuttle body with the position finger opposite the notch at the top of the shuttle race, release the latch and press the bobbin case back until the latch catches the groove near the end of the stud (see Fig. 8). Allow about two inches of thread to hang free.
To Set the Needle
¶ Turn the balance. wheel over toward you until the needle bar moves up to its highest point; loosen the screw (3, Fig 14, page 15) in the needle clamp and put the needle up into the clamp as far as it will go, with the long groove of the needle toward the left and the eye of the needle directly in line with the arm of the machine, then tighten the screw.
To Thread the Needle
¶ Pass the thread from the unwinder or from the spool on the right spool pin on the top of the machine, into the thread retainer ❶, down under from right to left between the tension discs ❷ into the thread take-up spring ❸, under the tension thread guard ❹ up and from right to left through the hole in the end of the thread take-up lever ❺ down through the eyelet ❻ down through the eyelet ❼ into the eyelet ❽ and from left to right through the eye of the needle ❾. ¶ Draw about two inches of thread through the eye of the needle with which to commence sewing.
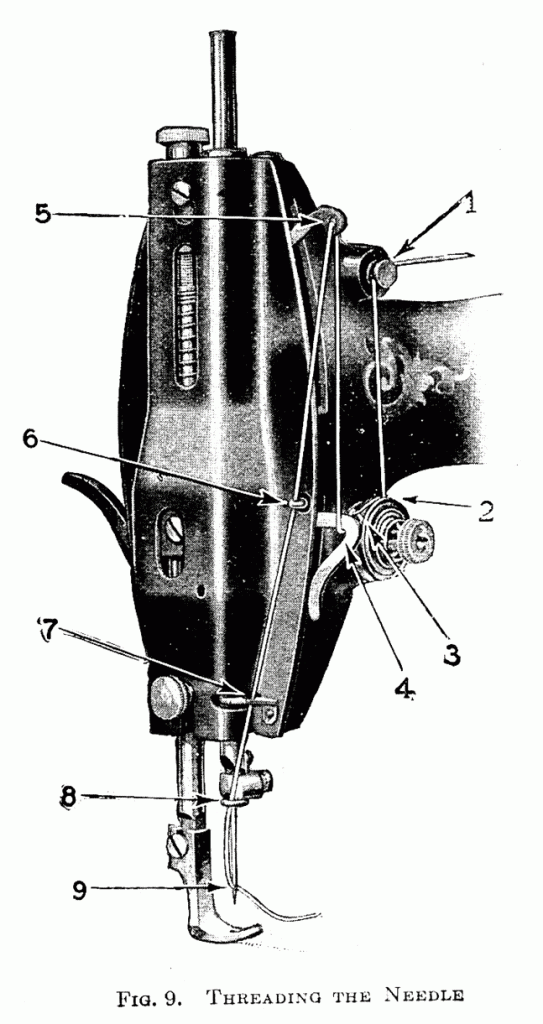
To Prepare for Sewing
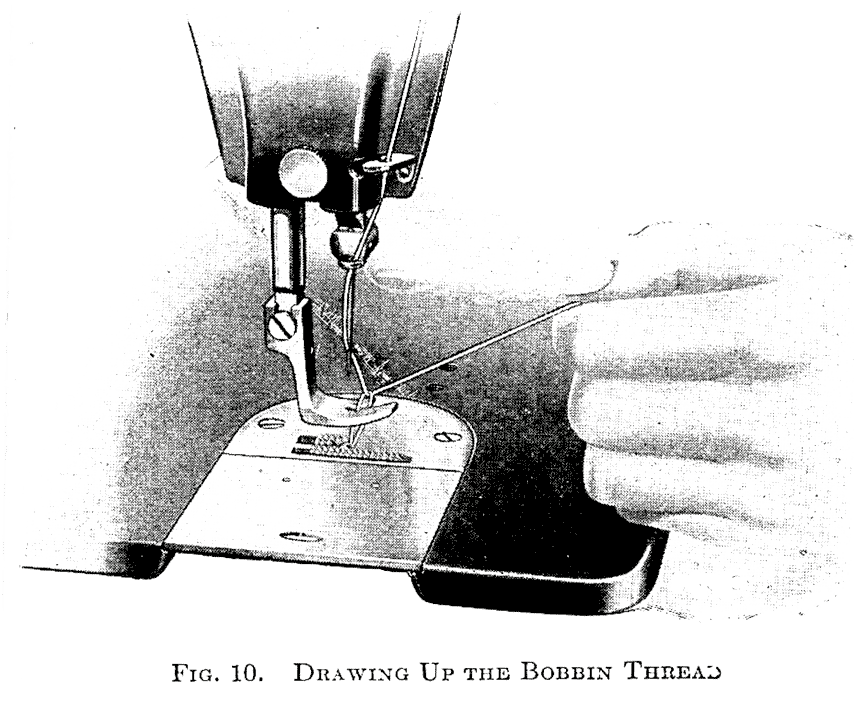
¶ With the left hand hold the end of the needle thread leaving it slack from the hand to the needle,turn the balance wheel over toward you until the needle moves down and up again to its highest point, thus catching the bobbin thread; draw up the needle thread and the bobbin thread will come up with it through the hole in the throat plate (see Fig. 10). ¶ Lay both threads back under the presser foot.
To Commence Sewing
¶ Place the material beneath the presser foot, lower the presser foot and commence to sew, turning the balance wheel over toward you.
To Remove the Work
¶ Let the thread take-up lever rest at its highest point, raise the presser foot, draw the work back and cut the threads close to the material.
Tensions
¶ For ordinary stitching the needle and bobbin threads should be locked in the centre of the thick- ness of the material, thus:
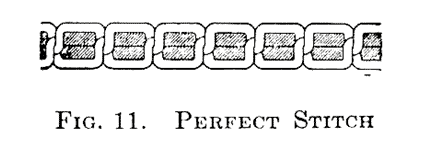
¶ If the tension on the needle thread is too tight, or if that on the bobbin thread is too loose, the needle thread will lie straight along the upper surface of the material, thus:
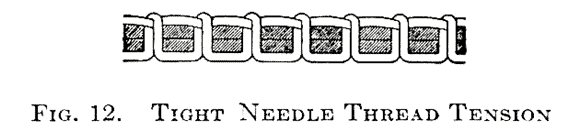
¶ If the tension on the bobbin thread is too tight or if that on the needle thread is too loose, the bobbin thread will lie straight along the under side of the material, thus:
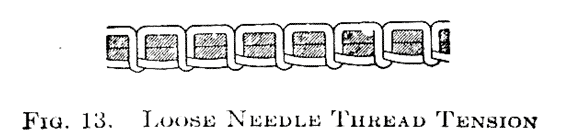
To Regulate the Tensions
¶ The tension on the needle thread should only be regulated when the presser foot is down. ¶ Having lowered the presser foot, turn the small thumb nut (2, Fig. 14) at the front of the tension discs over to the right to increase the tension. ¶ To decrease the tension, turn the thumb nut over to the left. ¶ The tension on the bobbin thread is regulated by the screw (1, Fig. 6) in the bobbin case tension spring. ¶ To increase the tension, turn the screw over to the right. To decrease the tension, turn the screw over to the left. ¶ When the tension on the bobbin thread has been once properly adjusted it is seldom necessary to change it, as a correct stitch can usually be obtained by varying the tension on the needle thread.
To Regulate the Length of Stitch
¶ The length of stitch is regulated by the thumb screw (4, Fig. 14) in the slot on the front of the upright part of the arm. ¶ To lengthen the stitch loosen the thumb screw and move it downward. ¶ To shorten the stitch loosen the thumb screw and move it upward. ¶ When the desired length of stitch has been obtained, tighten the thumb screw.
To Regulate the Pressure on Material
¶ The pressure on the material is regulated by the thumb screw (1, Fig. 14) on the top of the machine. ¶ To increase the pressure turn the thumb screw over to the right. ¶ To decrease the pressure turn the thumb screw over to the left. ¶ The pressure should be only heavy enough to enable the feed to move the work along evenly.
To Oil the Machine
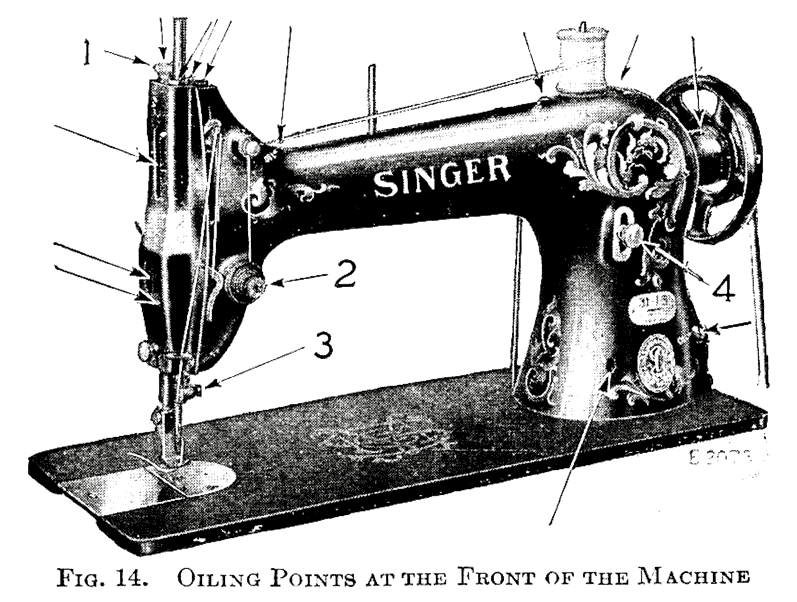
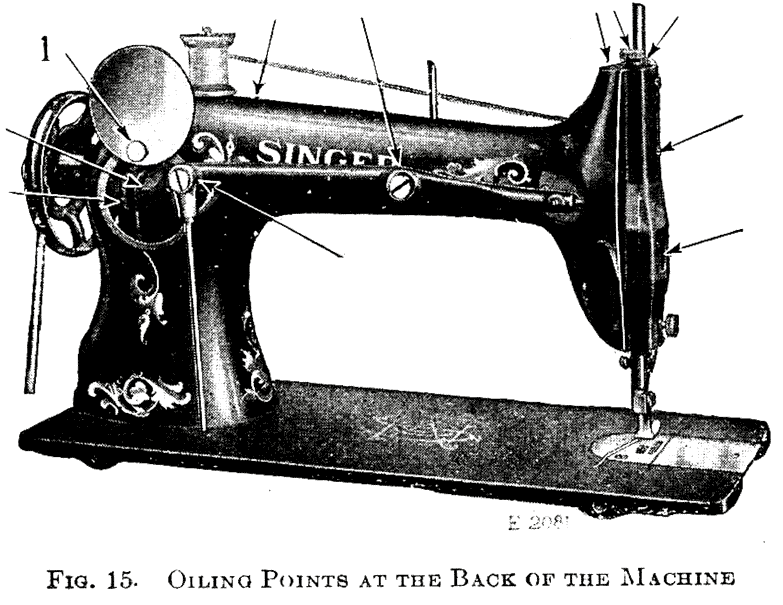
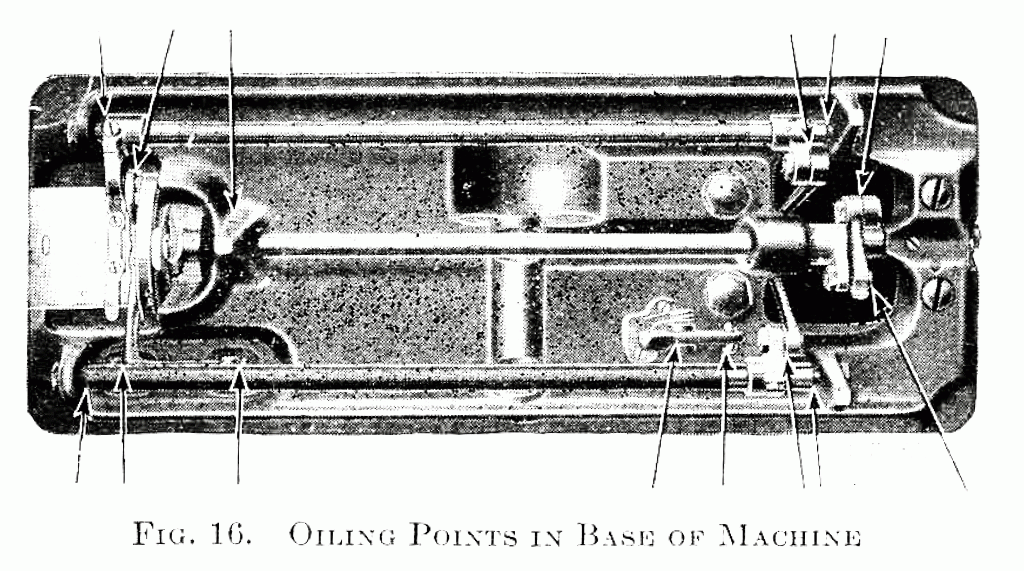
¶ The machine should be oiled at the places shown by arrows in Figs. 14, 15 and 16, and should be oiled frequently when in continuous use. the bearings at the base of the arm, remove the screw which is located at the extreme right of the arm and keep the oil reservoir filled with oil. ¶ When replacing the screw see that the leather washer is under the screw head and that the screw is tightened securely. ¶ Loosen the thumb screw (1, Fig. 15) in the round cover plate on the back of the machine, turn the cover plate up and oil the bearings which are thus uncovered, then replace the cover. back the machine on its hinges and apply oil at the places shown by arrows in Fig. 16, and all other places where there are parts in movable contact, then bring the machine into place. ¶ Oil should be regularly applied to the shuttle bearing in the shuttle race. ¶ Occasionally remove the face plate and apply oil to the bearings and joints thus uncovered.
Instruction for using SINGER SEWING MACHINE No.31-15
From 8268 Jan, 1916